Slurry pumps face very challenging operating conditions. An effective maintenance regime is thus critical for keeping them – and with them, the rest of the mine – performing as well as possible. We asked experts from Weir Minerals and KSB SupremeServ-GIW for their insight into some of the key issues.
By Jonathan Rowland
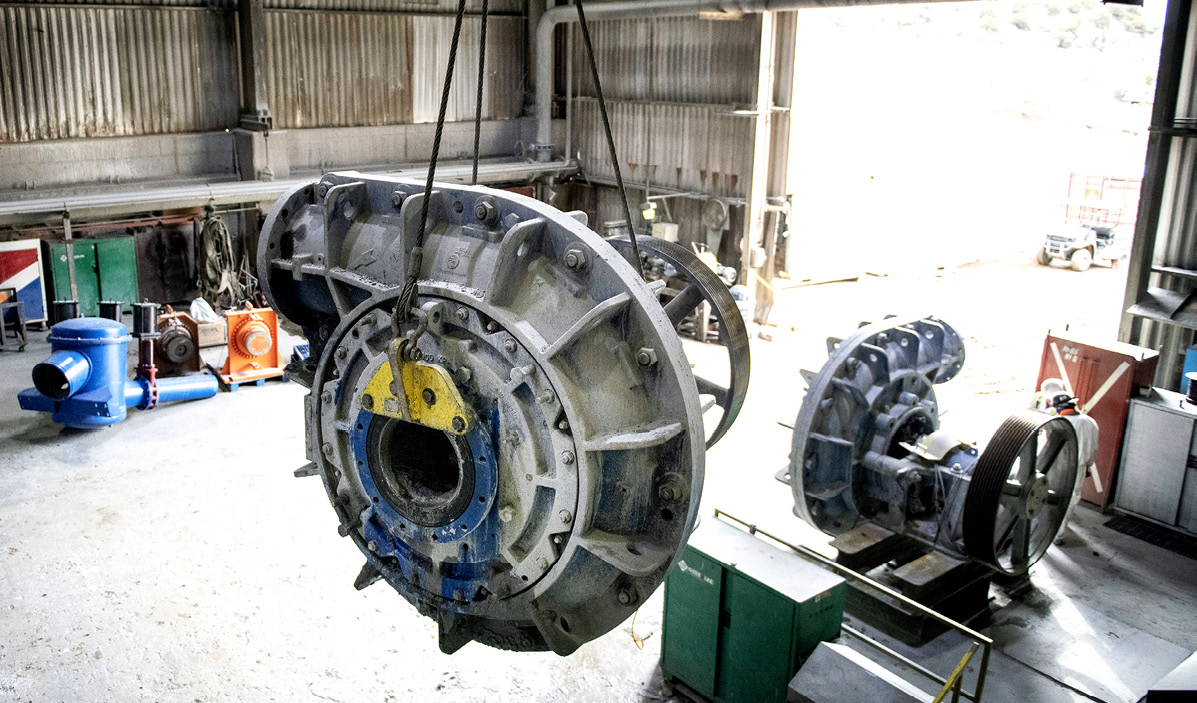
Slurry pumps face several challenges related both to their operating environment and service application. Mine sites offer harsh conditions for any machinery to work in: pumps must therefore be tough and robust to survive there. “Many of the biggest mine sites across the Americas are located in areas that are among the most hostile operating environments,” Chad Bauch, KSB SupremeServ-GIW service engineer, told North American Mining. “From the high altitudes of Chile, to the hot and humid climate of Panama, and the extreme winters of northern Canada, each of these unique operating environments presents its own challenges. Pump selection is therefore critical to achieving efficient and reliable operation.”
The hostile and remote locations of some slurry pumps installation also pose challenges through the operating life of the pump, added Sid Higdon, director of service at KSB SupremeServ-GIW. “General access to monitor and maintain the pump can pose major issues. This can create an ‘out of sight, out of mind’ situation, where routine maintenance is neglected.”
WEAR PROTECTION
Location is not the only issue when it comes to slurry pump operation and maintenance; the slurry these pumps handle can be abrasive and/or corrosive, noted Mark Woestman, product manager – centrifugal pumps at Weir Minerals. This again asks questions when it comes to pump selection:
“The challenge is to select and configure the pump with the appropriate materials to allow for even distribution of wear, thereby extending operating life and reducing downtime.”
There are three principles of wear protection, according to KSB SupremeServ-GIW’s Chad Bauch: pump selection, chemical makeup, and material hardness.
“Selecting the proper pump for the application is critical: pumps that are undersized have a high recirculating load, leading to unnecessary additional exposure to the slurry,” Bauch explained. “Selecting the proper material is equally important in combating the effects of corrosive wear and minimizing mechanical abrasion: for example, urethane wet end parts are often found in tailings systems because it’s excellent at preventing fine particle wear. However, urethane can be susceptible to chemical corrosion so, when using it, we must make sure the slurry is chemically neutral.”
Proper hardness of wear parts is the final part of the jigsaw and helps prevent mechanical abrasion. “The heat treatment process is critical in achieving proper hardness, while preventing parts becoming too brittle,” continued Bauch. “For example, the ladder pump on a dredge is expected to see large, dense particles make heavy impact with the wet end parts. If these are not of the proper hardness, the impact can cause cracking or breakage.”
The selection of wear materials should thus be based on “a thorough understanding of the specific characteristics of the slurry, pump operating conditions, and expected wear mechanisms,” concluded Woestman.
During pump operation, “we protect against wear via regular nose gap adjustments,” said Desmond Wilson, field service supervisor at KSB SupremeServ-GIW. “Leaving too long an interval between adjustment will cause premature wear on the suction liner and impellers, which can also have negative impact on the casing and hub liner. If the pump cannot be taken down for nose gap adjustment, it can be equipped with an adjustable suction liner to allow adjustment during operation.”
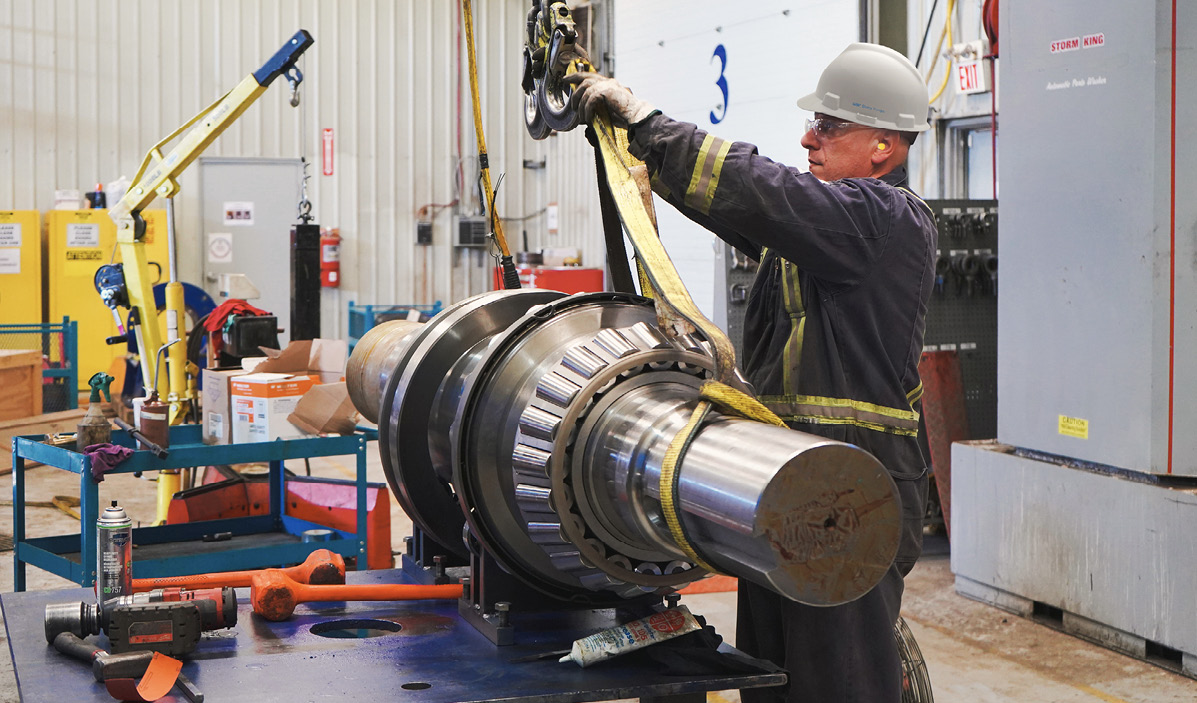
BEARING CHALLENGES
The bearing assembly is critical to the operation of any rotating equipment. There are however a range of factors that can contribute to bearing failure on a slurry pump. Avoiding these begins with the selection of high-quality bearings that can handle difficult operating conditions. These bearings must also be properly stored, handled and installed.
As should be clear at this point, however, challenges continue past proper selection and installation: improper lubrication, misalignment, overloading or excessive loads, and contamination are among the major operational issues that bearing assemblies face. “Needless to say, assessing what’s causing a particular problem isn’t always straightforward,” noted Woestman.
“Shortened bearing life can occur when the bearing size is not correct, or when the load conditions change from the original design,” said Wilson. “Cavitation, large solids, vibration, and other unusual pump conditions can further reduce bearing life by imparting additional loads. When it comes to lubrication, using an oil with the wrong viscosity can generate heat and cause bearing failure, as can underfilling and overfilling lubrication. Underfilling will result in lubrication loss and unit failure; overfilling will generate more heat and can aerate the oil which raises the level and can cause leakage.”
“Another key area when it comes to bearing maintenance is the shaft seal area,” said Higdon. “Properly packed and maintained stuffing box assemblies will prevent water or product from blowing back onto the bearing assembly, which is the leading cause of contaminant ingress and bearing failure.”
“Proper stuffing box and packing maintenance is a crucial step to prevent gland water from contaminating the bearing housing,” agreed Bauch. “The standard labyrinth seal with v-ring does a good job of keeping typical environment contaminants out of the bearing housing, but it cannot hold up to a spraying stuffing box. An upgrade to an Impro/Seal – which offers better sealing of the housing – can be offered for most pumps; however, it also cannot stand up to high pressure spray for extended periods of time. To provide a solution here, we have developed a dynamic flinger to be used with the Impro/Seal that prevents gland water from entering the bearing assembly when the pump is in operation.”
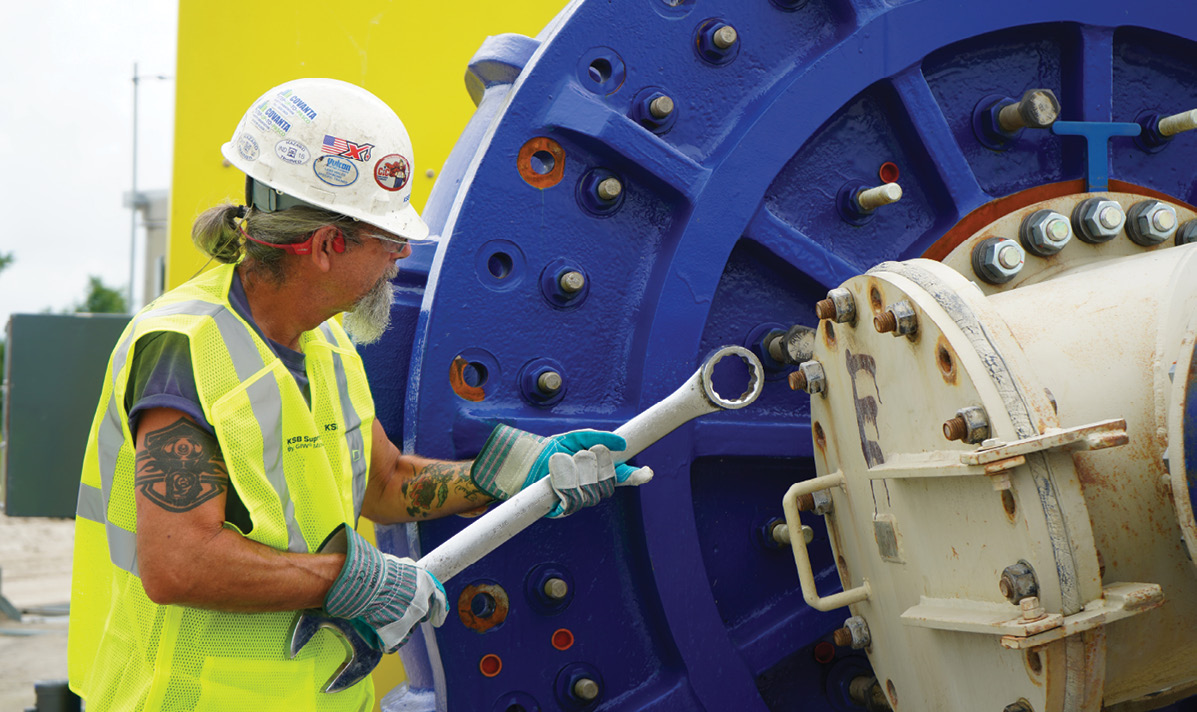
SIGNS OF A PROBLEM
“Operators should have an established baseline for flowrate, discharge pressure, vibration, sound, bearing temperature, and motor amperage,” explained Woestman. “Any significant changes outside these baseline conditions can indicate possible need for maintenance.”
Identifying and addressing such conditions is what makes regular checking and monitoring – however challenging the pump’s location – so essential, agreed all our experts. “There are a number of red flags that can indicate pump issues,” said Bauch. “Best practice predictive maintenance tasks, such as vibration monitoring, measuring differential pump head and bearing assembly temperature, and routine oil sampling, can give an early indication of a potential failure.”
“Proactive measures, such as implementing condition monitoring systems and following a preventative maintenance plan, can help minimize downtime and optimize pump performance,” agreed Woestman.
Recording and analyzing the vibration of a pump or other equipment, such as motors and gearboxes, is one important tool when it comes to identifying any potential problems. “When increased vibration is detected, monitoring equipment can be used to plot the signature of the vibration. This signature can then be used to identify what component may be in the early stages of failure,” explained KSB SupremeServ-GIW’s Higdon.
“Unusual vibrations can indicate problems like life misalignment, bearing wear, impeller damage, or other related issues,” added Woestman. “This data can be utilized to determine the remaining useful life of the pump internals, and maintenance can be planned accordingly.”
It’s this ability to pre-plan maintenance that is a particular benefit of vibration monitoring. “Monitoring programs are especially valuable when baseline levels are recorded on new equipment. Routine readings can then trend the equipment’s health over time. This gives the maintenance team some ability to plan repairs around shutdowns to increase uptime,” continued Higdon.
“Ultimately, good maintenance practices do prevent unplanned downtime, and vibration monitoring data can be used to establish such preventative maintenance schedules,” concluded Woestman. “However, it should be understood and carried out as part of broader maintenance strategy that includes other inspection methods, lubrication practices, and operational considerations.
PUMPS 4.0?
“Digitalization in pump maintenance will continue evolving with advancements in connectivity, data analytics, AI, and simulation technologies,” predicted Woestman. “This will lead to more proactive, data-driven maintenance strategies, optimized performance, and increased reliability of pumps.”
One example of this can be seen in improving maintenance practices through remote monitoring of equipment that might (to return to a point made earlier on in this article) take significant time and effort to access manually. This continuous recording and monitoring across a range of data points enables much more accurate tracking of equipment health – and thus supports the creation of more robust maintenance programs. For example, warning levels can be established for a range of metrics, including vibration levels, bearing temps, and motor amperage, which give operators notice so equipment can be shut down before catastrophic failure occurs.
“I see this level of monitoring becoming easier for all customers to obtain moving forward, providing an overall increase in what can be captured and converted into useable information,” said Higdon.
Higdon’s colleague, Desmond Wilson, concluded with the field engineer’s perspective: “Imagine you’re an operator and you can use your phone to scan a QR code on the pump casing to get information on what the flow rate and RPM should be, as well as gland water requirements. Or you’re a maintenance technician and you scan the code to see a cross-sectional drawing of the part you’re looking for and the material master associated with it. Or maybe you would like to see the manual to see the steps for wet end maintenance. This is on the forefront of what is coming soon to sites near you.”